However, the advanced capabilities of these PLCs bring forth significant safety considerations. In environments where machinery and processes can pose risks to human operators and equipment, the safety aspect of PLC operations becomes paramount. Ignoring these safety concerns can lead to not only equipment damage and production downtime but also serious workplace accidents.
The purpose of this article is to delve into the safety dimension of Omron PLC operations. We aim to provide actionable insights and best practices to ensure safe operations, thereby safeguarding personnel, equipment, and processes. Understanding these safety measures is crucial for anyone involved in operating, maintaining, or managing PLC-controlled systems.
I. Understanding Omron PLCs
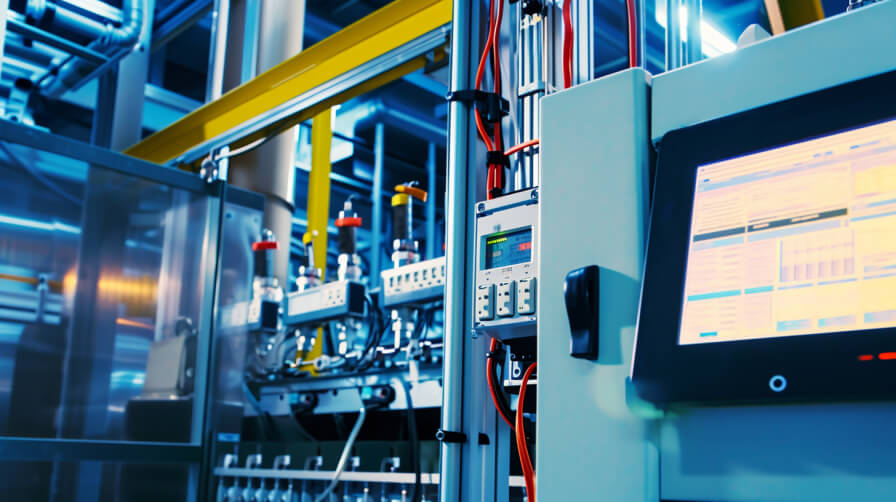
Omron PLCs operate by continuously monitoring input devices and making decisions based on custom-programmed logic to control output devices. Essentially, they read signals from sensors, process these signals according to the programmed instructions, and output commands to execute actions such as starting or stopping motors, opening or closing valves, or displaying data.
Key features of Omron PLCs that are relevant to safety include:
- Real-Time Operation: They operate in real-time, ensuring timely responses to input conditions.
- Diagnostic Functions: Advanced diagnostics help in identifying issues before they escalate into safety hazards.
- Interlocking and Safety Routines: Built-in features for interlocking and executing safety routines to prevent dangerous conditions.
Common applications in industry involve scenarios where precision and reliability are critical, such as:
- Automated assembly lines.
- Process control in chemical plants.
- Material handling and packaging in logistics centers.
II. Identifying Potential Safety Hazards
Safety hazards in PLC operations can stem from various sources, including:
- Electrical Hazards: Issues such as short circuits or improper wiring can lead to electrical accidents.
- Mechanical Failures: Failures in connected machinery, due to either malfunctioning components or PLC programming errors.
- Human Error: Misinterpretation of PLC signals or incorrect programming.
III. Best Practices for Safe PLC Operations
Ensuring safety in Omron PLC operations involves a combination of strict protocols and continuous education. The following best practices are essential:
- Regular Maintenance and Inspection Protocols: Regularly scheduled maintenance is crucial for identifying potential issues before they escalate. This includes inspecting wiring, testing input/output signals, and verifying the proper functioning of all connected devices. Preventative maintenance schedules should be adhered to rigorously.
- Training and Education for Operators and Maintenance Staff: Comprehensive training programs ensure that all personnel involved with PLCs understand how they work and are aware of potential risks. Training should cover not only basic operation but also emergency procedures and troubleshooting techniques.
- Implementing Fail-safes and Redundancy Features: Fail-safes, such as automatic shutdown mechanisms in case of signal loss or inconsistency, are vital. Redundancy, where critical components or systems have backups, can also be incorporated to enhance safety.
IV. Advanced Safety Features in Omron PLCs
Omron PLCs are equipped with several advanced safety features designed to mitigate risks:
- Integrated Safety Functions: Many Omron PLC models come with built-in safety functions like emergency stop, safety door monitoring, and two-hand control. These features are designed to immediately respond to hazardous conditions.
- Network Safety Protocols: Utilizing safety networks, like Safety over EtherCAT or FSoE (Fail-Safe over EtherCAT), which allow for real-time monitoring and quick response to safety-critical signals.
- Advanced Diagnostics: These features enable operators to quickly identify and address issues, reducing the risk of accidents due to equipment malfunction.
V. Compliance with Safety Regulations
Safety in PLC operations is not just a matter of best practices but also of legal compliance. Various international and regional standards govern the safety of automated systems, including PLCs.
- International Standards: Standards such as ISO 13849 and IEC 61508 provide guidelines for the safety of machinery and functional safety of electrical/electronic/programmable electronic safety-related systems, respectively.
- Regional Compliance in North America and Europe:
- In North America, standards like ANSI/RIA R15.06 and NFPA 79 are pertinent for industrial machinery safety.
- In Europe, directives such as the Machinery Directive (2006/42/EC) and standards like EN 62061 and EN ISO 13849-1 are crucial for compliance.
VI. Troubleshooting Common Safety Issues
Troubleshooting is an integral part of maintaining the safety integrity of Omron PLC systems. Here are some guidelines:
- Guidance on Identifying and Resolving Frequent Safety Concerns:
- Regularly monitor system logs for error messages or unusual activity.
- Conduct simulated fault conditions to ensure that safety features activate correctly.
- Use diagnostic tools provided by Omron to pinpoint specific issues.
- Preventative Measures to Avoid Recurring Problems:
- Implement a checklist for routine inspections and adhere to it strictly.
- Update PLC software and firmware regularly to ensure the latest safety features are active.
VII. Case Study: Successful Safety Implementation
A case study showcasing successful safety implementation involves a manufacturing facility that upgraded to Omron PLCs. After experiencing a minor incident due to a mechanical fault, the facility implemented several of Omron’s advanced safety features, including integrated safety functions and network safety protocols. As a result, the facility saw a significant reduction in incident rates and improved overall safety compliance.
VIII. Conclusion
This article has explored the critical aspects of ensuring safety in Omron PLC operations, from understanding the basics to complying with international safety standards. The key takeaway is the importance of continual learning and adaptation in safety practices. As technology evolves, so too should our approach to safety in industrial automation.
If you need immediate technical support or are looking to purchase genuine OMRON industrial automation products, feel free to contact us at info@ikwoco.com. With over 30 million worth of product inventory, our team at ikwoco is dedicated to providing quick quotations, delivery, and technical support for OMRON products.